Guiding Systems
Your Guide to Strip Guiding Systems
IMS strip guiding systems (SGSs) are an ideal way to mechanically correct the position of a moving strip, or to maintain the strip’s position on the machine. The advantages of using a custom SGS include achieving straight edge coils, operating at higher line speeds, and preventing product damage so you can achieve higher repeatability, better product quality, and improved productivity.
SGSs can be used on Annealing & Pickling Lines, Cold Rolling Mills, Continuous Hot Dip Galvanizing Lines, Cut-to-Length Processing Lines, Slitting Lines, Tension Leveling Lines, and on any other type of strip processing line.
An SGS can compensate for poor coil wrap quality, misalignment of rolls or machinery elements, uneven roll wear and pinch roll pressure, and inadequate tension.
How the Technology Works
An SGS operates by using a 3-step process that consists of:
- Strip traveling through the process line
- Sensor detecting the current strip position
- Controller processing the current strip location, calculating the desired position, and sending the signal to the Actuator, which can be a servo-hydraulic or electro-mechanical system
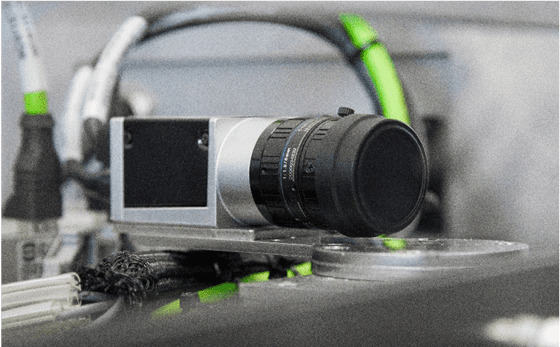
Typical Strip Guiding Layout
Depending on the application, an SGS can be placed at many points throughout a production line.
Processes requiring the most accurate strip position include Slitting, Side Trimming, Cut to Length, Coating, Laminating, and Recoiling. At IMS, our unique combination of field expertise can help you determine the best location for system placement.
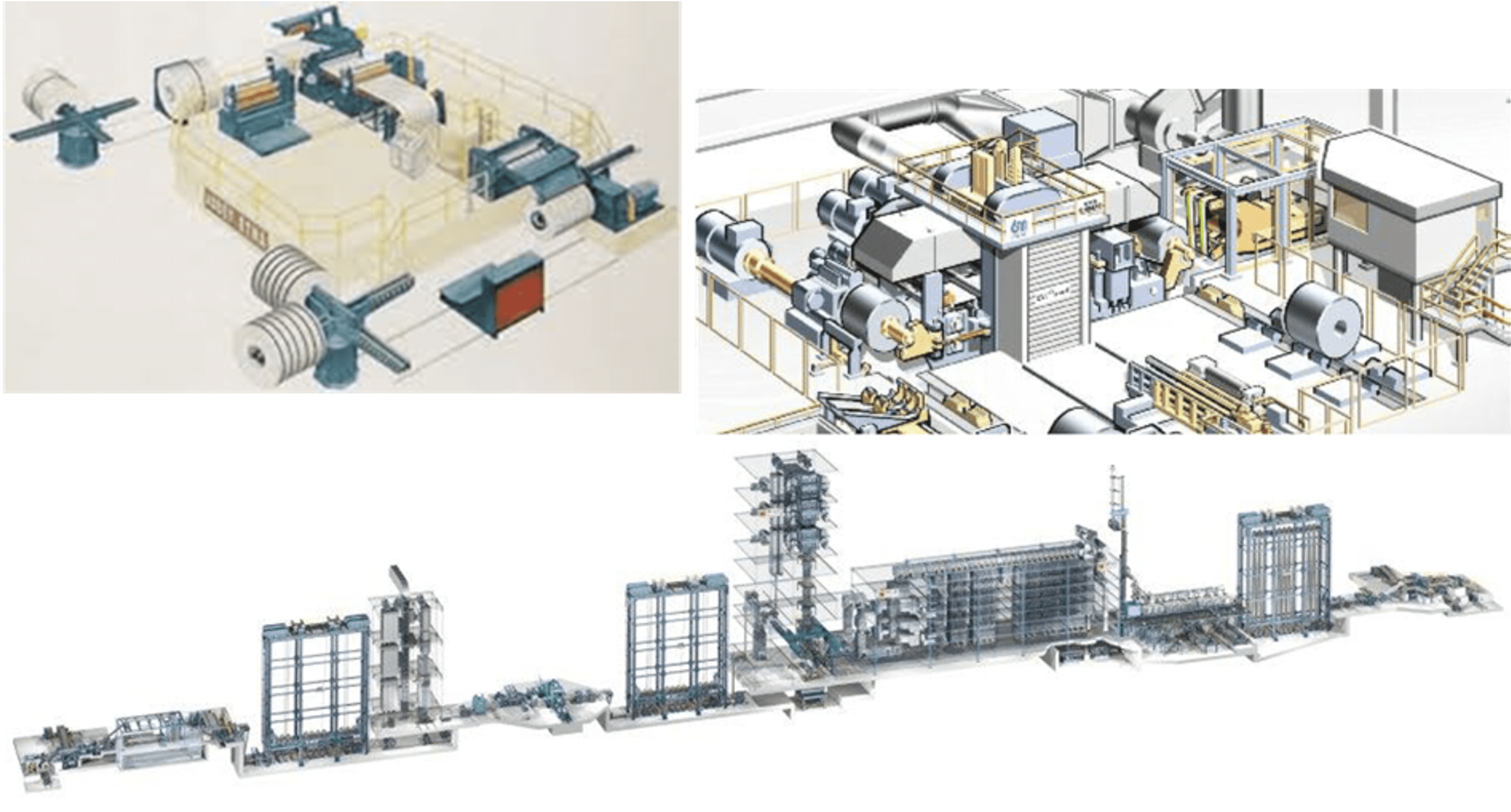